Designed by Communitecture
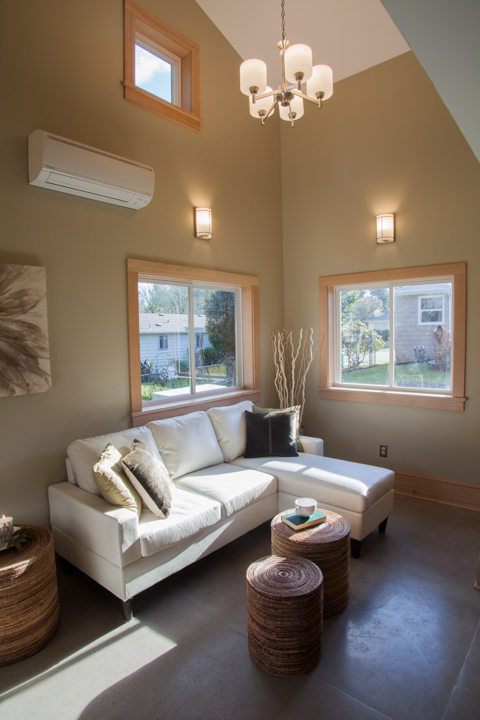
Client Needs
Bill and Mary didn’t just need an ADU – they needed a custom mini home like no other in the Portland area. With serious chemical sensitivities, Mary would have to personally vet every material used in the construction process to ensure a safe and comfortable environment where she and Bill could enjoy spending time together for years to come. See the before picture »
Remodel Highlights:
- Thanks to the use of low-VOC alternatives to many traditional building products – including drywall mud, paint, concrete sealant, building paper, and even formaldehyde-free insulation – Mary enjoys time in the home without pain or discomfort. “We spend the majority of our time together down here, and it’s a dreamy place,” the couple said.
- The 650-square-foot home is always filled with fresh, clean air thanks to its Heat Recovery Ventilation (HRV) system, which continually pulls in fresh air while retaining the heat from “stale” air on its way out.
- Throughout the build, the team and homeowners tracked the product vetting process on a shared Google Sheet, keeping everyone organized and on the same page.
Client Testimonial
We needed someone who would be flexible and curious about doing a clean build, and Bert really rose to the challenge. He’s personable and incredibly organized; he kept a spreadsheet of all the materials we were vetting and met with us on a weekly basis. We wouldn’t say it was an easy project – and I don’t think Bert would either – but I don’t think we could’ve done it without him. I would especially recommend him for anyone who’s trying to do something non-traditional or unique. He’s determined, detail-oriented, and pleasant to be around.
-Bill & Mary
Notes for Architects:
- To minimize off-gassing and ensure a safe living space for Mary, the team meticulously vetted each product used, working closely with healthy home consultant Paula Baker-Laporte of EcoNest Architecture. Paula recommended products, contractors sourced them, and she and Mary approved each product before it was brought into the building process.
- Preventing mold growth was another priority. So, using a heavy-duty vapor barrier beneath the slab ensured no ground moisture would percolate into the concrete. A rainscreen system was also used to hold the siding out from the building and allow the structure to breathe.
- To comply with the Energy Efficiency Additional Measures Requirements, the team employed a combination of fiberglass and rigid insulation on the roof. Traditional fiberglass insulation was placed between the rafters and rigid insulation was placed on top of the roof deck – and the additional rigid installation made a dramatic difference in temperature as soon as it was installed.
- With the ADU set back by nearly 200 feet, the team used directional drilling to run the water and sewer lines out to the street. Because the sewer line had to maintain a downward slope all the way to the street, this was no easy feat. But the team was able to make it by 6 inches, saving the homeowners thousands of dollars and maintaining their landscaping.